10 Best Tool Tracking Tags for Construction Equipment Management in 2025
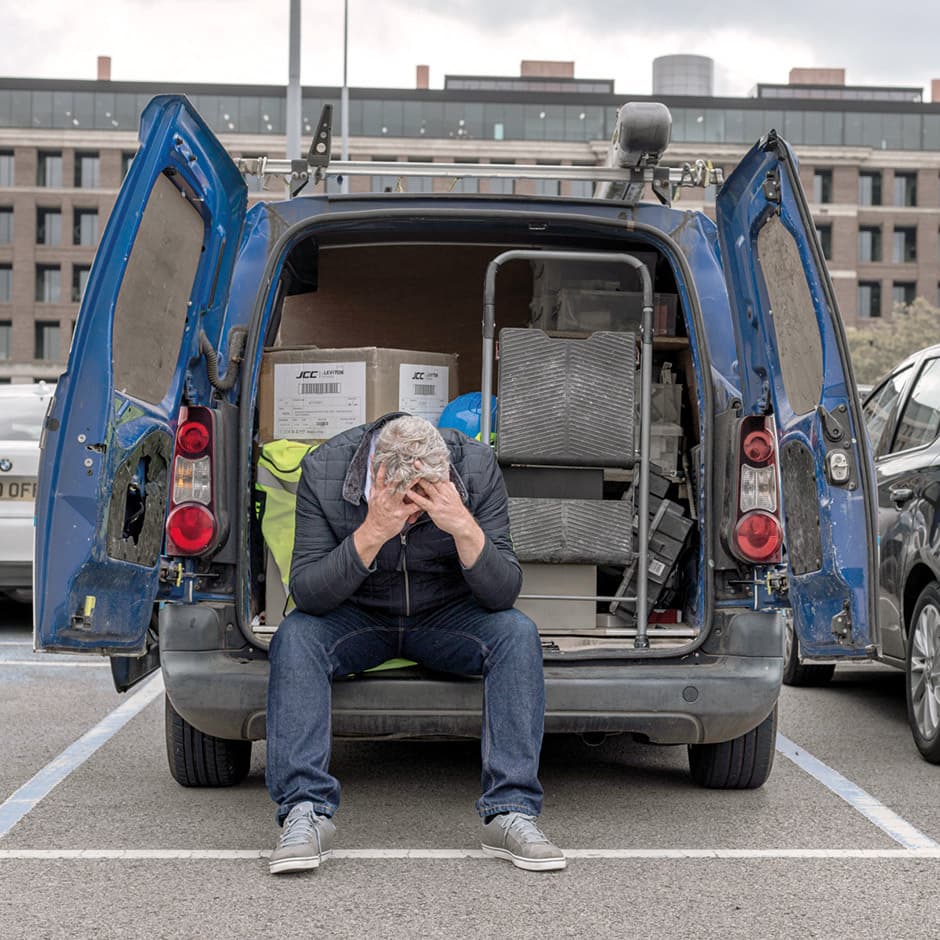
The Complete Guide to Tool Tracking Tags for Construction Equipment
In May 2024, a Virginia carpenter's story made headlines when his strategic use of Apple AirTags led police to recover not only his stolen tools but an estimated $3-5 million worth of equipment stolen from hundreds of businesses and contractors. This real-world example dramatically illustrates what construction businesses have known for years: tool theft is a massive, expensive problem—and modern tracking technology offers a powerful solution.
On busy construction sites and factory floors, keeping track of valuable tools has always been challenging and often leads to significant financial losses. The good news? Advanced tool tracking tags are revolutionizing how companies monitor their equipment investments. Let's explore how these small but powerful devices are transforming equipment management in 2025.
- Understanding Tool Tracking Technology
- The Financial Impact of Poor Tool Management
- Key Benefits of Inventory Control Tags
- Limitations of Traditional Inventory Systems
- GPS Tracking Solutions for Construction Equipment
- Essential Features for Construction Tool Tags
- Real-World Success Stories
- Software Integration Options
- Emerging Trends in Tracking Technology
- Implementation Guide for Your Business
Understanding Tool Tracking Technology
Tool tracking tags have fundamentally transformed how businesses approach asset management. These compact devices attach to tools and equipment, enabling real-time location monitoring, usage tracking, and maintenance scheduling. They leverage various technologies to create comprehensive visibility:
- RFID Tags: Ideal for inventory management within confined areas
- Bluetooth Beacons: Perfect for moderate-range indoor tracking
- UWB (Ultra-Wideband): Providing centimeter-level precision for critical assets
- GPS Tracking Systems: Delivering wide-area coverage for construction equipment
- Cellular-Connected Trackers: Offering unlimited range with real-time updates
- Network-Leveraging Tags: Using existing networks like Apple's Find My for cost-effective tracking
The most sophisticated 2025 solutions, particularly those utilizing Apple's Find My network and similar technologies, transcend traditional asset management capabilities. Rather than simply documenting what you own, they create a dynamic digital connection between physical assets and management systems.
"The recent Howard County case where AirTags helped recover 15,000 stolen tools worth up to $5 million demonstrates how even simple tracking technology can have an enormous impact on theft prevention and recovery." — Construction Security Association, 2025
The Financial Impact of Poor Tool Management
Effective tool inventory management isn't just about organization—it's a critical financial imperative, especially for construction and manufacturing operations where equipment represents substantial capital investment.
The numbers tell a compelling story:
- 5-10% annual tool loss: Construction companies typically lose this percentage of their tool inventory to theft, misplacement, or damage each year
- $100-$300 per hour: The cost of downtime when equipment failure halts production
- 90 hours wasted annually: The average time workers spend searching for missing tools per year
- $5,000-$50,000: Typical annual losses for small to mid-sized contractors due to tool theft alone
- 42% project delay rate: Nearly half of construction projects face delays related to equipment availability issues
Beyond these direct costs, poor tool management creates cascading effects throughout your business: project delays, quality issues, reduced workforce productivity, client dissatisfaction, and increased insurance premiums. Comprehensive inventory management doesn't just track assets—it protects your bottom line, optimizes utilization, ensures proper maintenance, and maximizes ROI on equipment investments.
Key Benefits of Inventory Control Tags
Implementing robust tool tracking systems with inventory control tags delivers measurable benefits across operations:
1. Dramatic Reduction in Tool Loss and Theft
With real-time location awareness, companies report significant decreases in missing equipment. The average implementation results in 70% fewer lost or stolen tools—a benefit vividly illustrated by the Virginia carpenter whose AirTags led authorities to a massive tool theft operation.
2. Enhanced Workforce Productivity
When workers can quickly locate necessary equipment, productivity soars. Research indicates that effective tool tracking systems save 2-4 hours per worker weekly—time previously wasted searching for missing items.
###.3. Optimized Tool Utilization
Usage data reveals equipment utilization patterns, identifying underused assets and opportunities for resource sharing. This prevents unnecessary purchases and maximizes value from existing inventory, with typical utilization improvements of 25-35%.
4. Data-Driven Maintenance
Usage tracking enables maintenance scheduling based on actual utilization rather than arbitrary calendars. This approach extends equipment lifespan by 15-20% while reducing emergency repairs by approximately 40%.
5. Streamlined Compliance Management
For regulated industries, tracking systems simplify documentation and reporting requirements. Companies report 65% reductions in compliance-related administrative time and significant decreases in safety violations related to equipment.
Limitations of Traditional Inventory Systems
Before modern tracking solutions, companies faced significant obstacles in managing their tool inventories:
Paper-Based Systems Fail Under Pressure
Manual documentation and spreadsheets consistently break down in dynamic work environments, resulting in incomplete records, data entry errors, and information that's perpetually outdated.
Limited Visibility Creates Blind Spots
Without real-time tracking, managers had no accurate picture of equipment location or utilization patterns, leading to resource misallocation and poor planning decisions.
Reactive Maintenance Increases Costs
Traditional systems could only address equipment failure after it occurred, driving up repair costs and creating avoidable downtime instead of enabling preventive maintenance.
Accountability Gaps Create Conflict
Without automated tracking, establishing responsibility for tools became contentious, often creating workplace tension and blame-shifting when items went missing.
Redundant Purchasing Wastes Capital
Uncertainty about equipment availability frequently led to unnecessary duplicate purchases, wasting financial resources and creating storage challenges.
GPS Tracking Solutions for Construction Equipment
The construction industry has emerged as a primary beneficiary of advanced tool tracking technology. With multiple job sites, diverse equipment needs, and high-value assets, construction operations face unique tracking challenges that modern GPS systems effectively address.
Construction companies typically manage assets ranging from small power tools to heavy machinery across various locations and teams. In this environment, GPS tracking for construction equipment provides essential visibility that directly impacts project timelines and financial performance.
Organizations implementing construction equipment tracking systems consistently report remarkable outcomes:
- 35% reduction in replacement tool expenditures
- 20% improvement in equipment utilization rates
- 45% decrease in time spent searching for equipment
- 25% fewer project delays related to equipment availability issues
- 78% reduction in tool theft incidents after full implementation
Essential Features for Construction Tool Tags
The most effective construction equipment tracking GPS solutions incorporate these critical features:
Environmental Durability
Construction environments demand tracking devices built to withstand dust, moisture, impacts, and temperature fluctuations. Look for IP67 or higher ratings for critical equipment.
Extended Battery Performance
Tags used on construction assets should deliver multi-year battery life to minimize maintenance requirements and ensure continuous protection.
Multi-Technology Connectivity
Superior solutions offer layered connectivity options, including Bluetooth for proximity tracking and cellular/network options for remote monitoring capabilities.
Geofencing Capabilities
The ability to establish virtual perimeters around authorized locations with automatic alerts when equipment moves outside boundaries is essential for theft prevention.
Integration Flexibility
Seamless connection with existing management platforms ensures smooth data flow between tracking devices and administrative systems.
Tamper-Resistant Design
To counter deliberate theft, effective tags incorporate features that make unauthorized removal or disabling difficult without triggering alerts.
Real-World Success Stories
Virginia Carpenter's AirTag Recovery Leads to Major Bust
In January 2024, after experiencing multiple tool thefts, a 43-year-old Virginia carpenter installed Apple AirTags in his remaining equipment. When thieves struck again, he tracked his property to a storage facility where police discovered not only his tools but approximately 15,000 stolen items worth between $3-5 million, taken from hundreds of businesses and contractors across multiple counties. This remarkable case demonstrates how even simple tracking technology can disrupt major theft operations.
National Construction Contractor
A large contractor implemented Ultra-Wideband tracking across their equipment inventory, achieving:
- 42% reduction in annual tool replacement expenditures
- 3.5 hours saved per worker weekly (previously spent searching for equipment)
- 22% improvement in preventative maintenance compliance
- Complete ROI within 9 months of implementation
Regional Mechanical Contractor
A mid-sized mechanical contractor deployed a hybrid RFID/Bluetooth solution to track their specialized tools:
- Tool theft declined by 78% in the first year
- Equipment utilization increased by 34%
- Administrative time on inventory management dropped by 65%
- Annual audit process reduced from two weeks to three days
Global Manufacturing Facility
A manufacturing operation implemented tracking technology across multiple facilities:
- Production downtime from missing tools decreased by 31%
- Workflow efficiency improved by 17%
- Annual savings of $245,000 on replacement tools
- Complete elimination of safety violations related to missing equipment
Software Integration Options
The true power of tracking tags emerges when they seamlessly connect with comprehensive management software. This integration creates a system where physical tool movements automatically update inventory records, trigger maintenance alerts, and inform resource planning.
Modern tool management software typically offers:
- Real-time dashboards displaying equipment status and location
- Automated checkout/check-in procedures
- Maintenance scheduling based on actual usage
- Analytical tools to optimize utilization
- Mobile interfaces for field-based management
- API connections to enterprise systems
Key Selection Criteria
When evaluating software solutions, prioritize:
1. Scalability The platform should accommodate growth in both inventory size and organizational complexity.
2. User Experience Intuitive interfaces minimize training requirements and encourage system adoption.
3. Customization Options Different industries require tailored approaches to data collection and reporting.
4. Mobile Functionality Field access through mobile applications ensures the system functions where your tools are actually used.
5. Integration Capabilities Open APIs facilitate connections with existing business systems like ERP or procurement platforms.
6. Security Features Robust data protection safeguards information about your valuable assets.
Emerging Trends in Tracking Technology
Tool tracking technology continues to evolve rapidly, with several innovations poised to further transform equipment management:
Miniaturization
Advances in component design are creating increasingly compact tracking devices suitable for smaller tools previously difficult to monitor.
Power Efficiency Breakthroughs
Next-generation power management technologies now deliver multi-year or even decade-long battery life for passive tracking devices.
Mesh Network Architecture
Connected tracking systems now form self-healing networks that extend coverage and enhance reliability in complex environments.
Environmental Monitoring
Beyond location tracking, newer tags incorporate sensors that monitor conditions affecting tool performance and safety.
AI-Enhanced Analytics
Artificial intelligence applications now provide predictive insights for maintenance planning and utilization optimization.
Implementation Guide for Your Business
Step 1: Conduct a Tool Inventory Assessment
- Document all existing tools and equipment
- Categorize assets by value, mobility, and criticality
- Identify high-risk or frequently misplaced items
Step 2: Define Your Tracking Objectives
- Theft prevention and recovery
- Utilization optimization
- Maintenance management
- Compliance requirements
- Workforce efficiency
Step 3: Select Appropriate Tracking Technology
- Match tracking technology to specific asset classes
- Consider environmental conditions
- Evaluate battery life requirements
- Assess connectivity needs
Step 4: Develop Implementation Protocols
- Create standardized tagging procedures
- Establish responsibility for system management
- Define alert parameters and response protocols
- Design training programs for all users
Step 5: Measure and Optimize Results
- Track key performance indicators
- Gather user feedback
- Regularly review and refine the system
- Expand coverage as ROI is demonstrated
Conclusion: Transforming Asset Management Through Technology
The evolution from manual inventory tracking to intelligent monitoring systems represents more than a mere upgrade—it fundamentally transforms how businesses conceptualize and manage physical assets. Equipment and tools transition from static inventory items to dynamic, data-generating components of an interconnected system.
For forward-thinking organizations, this transformation delivers not just operational improvements but genuine competitive advantages. The insights derived from comprehensive tracking systems inform strategic decisions about resource allocation, capital investments, and operational planning.
As technology advances and implementation costs decline, sophisticated tracking solutions are becoming accessible to companies of every size, democratizing access to enterprise-level asset management capabilities. The relevant question is no longer whether to implement tracking technology, but rather which solution best aligns with your specific operational needs.
By embracing these innovations, organizations can maximize equipment investments, enhance operational efficiency, and strengthen competitive positioning in increasingly challenging markets.
This article was prepared by AirPinpoint, a leader in asset tracking solutions. Want to learn more about construction equipment tracking systems? Contact our team today for a free consultation on implementing theft-prevention technology for your valuable tools.